In the realm of sustainable practices and eco-conscious innovation, the rice hull charcoal making machine stands as a remarkable testament to human ingenuity. It represents a powerful tool in the quest for both environmental preservation and resource optimization. In this article, we will delve into the intricacies of this extraordinary piece of machinery, exploring its inner workings, benefits, and its role in promoting a greener future.
The Ingenious Design
At its core, the rice husk charcoal making machine is a marvel of engineering. It is specially crafted to transform rice hulls, often considered waste, into valuable charcoal. This process is carried out with precision and efficiency, making the most of every resource.
The machine operates in a series of carefully orchestrated steps, each contributing to the final result. First, the rice hulls are collected and loaded into the machine’s hopper, where they undergo a process known as pyrolysis. In this step, the rice hulls are subjected to high temperatures in the absence of oxygen, causing them to break down and release gases. These gases are then captured and used as an energy source, ensuring that nothing goes to waste.
The remaining residue from the pyrolysis process is the coveted rice hull charcoal, which can be used for various applications, from heating to agriculture. Its porous structure and high carbon content make it an ideal choice for soil improvement and water purification.
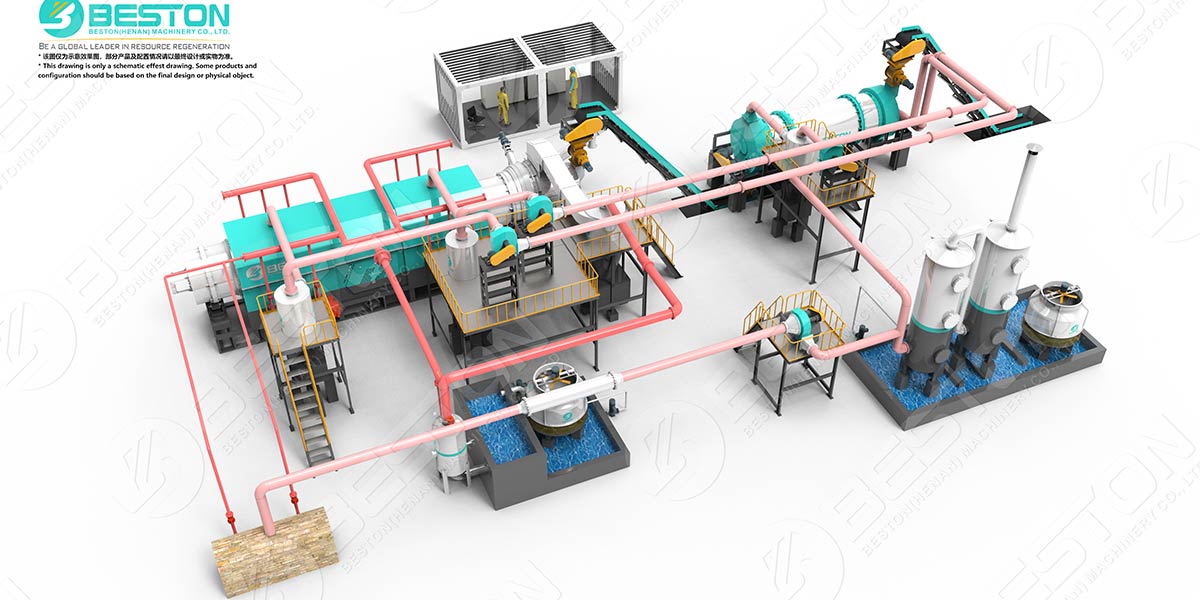
The Environmental Impact
One cannot overstate the significance of the rice hull charcoal making machine when it comes to environmental sustainability. By harnessing the potential of rice hulls, which would otherwise be discarded, it reduces the strain on landfills and minimizes the release of harmful greenhouse gases associated with their decomposition.
Furthermore, the utilization of pyrolysis as the primary conversion method is key to its eco-friendliness. Unlike traditional methods of charcoal production that rely on deforestation, the rice hull charcoal making machine operates with a significantly lower carbon footprint. This not only preserves our precious forests but also mitigates the effects of deforestation on climate change.
Versatility in Application
The versatility of the wood charcoal making machine is another factor that sets it apart. Beyond its primary function of producing charcoal, it can be adapted for various purposes within different industries. Let’s explore some of these applications:
1. Agriculture
Rice hull charcoal, enriched with carbon and essential minerals, has proven to be a boon for agriculture. When incorporated into soil, it improves its structure and water retention capacity. This, in turn, enhances crop growth and yield. Its porous nature also acts as a natural habitat for beneficial microorganisms.
2. Energy Generation
As mentioned earlier, the byproducts of the pyrolysis process, such as syngas, can be harnessed for energy generation. This dual functionality not only reduces the energy consumption of the machine itself but also contributes to the overall energy efficiency of the system.
3. Water Treatment
Activated carbon derived from rice hull charcoal is highly effective in water treatment processes. Its porous surface can adsorb impurities and contaminants, making it an excellent choice for purifying water in both industrial and domestic settings. More information on palm kernel shell charcoal making machine here.
Cutting-Edge Technology
What makes the rice hull charcoal making machine truly remarkable is its incorporation of cutting-edge technology. With advancements in automation and control systems, these machines can be operated with minimal human intervention, optimizing efficiency and reducing the margin for error.
Moreover, many of these machines are equipped with real-time monitoring and data collection capabilities. This allows operators to track the performance of the machine, identify any potential issues, and make necessary adjustments promptly.
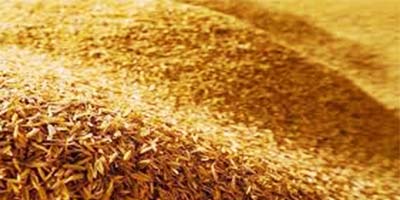
The Economic Viability
From an economic standpoint, investing in a rice hull charcoal making machine can be a sound decision. While the initial cost may seem substantial, the long-term benefits far outweigh it. The ability to convert rice hulls, a waste product, into a valuable resource opens up new revenue streams and reduces waste disposal costs.
In regions where rice production is a dominant agricultural activity, the machine’s economic viability is even more pronounced. It not only provides an additional source of income for farmers but also contributes to job creation within the community.
A Greener Tomorrow
In conclusion, the rice hull charcoal making machine is an exemplar of sustainable technology. Its ingenious design, eco-friendly operation, and versatility make it a valuable asset in the pursuit of a greener and more sustainable future. By turning a waste product into a valuable resource, it not only benefits the environment but also offers economic opportunities to individuals and communities worldwide. As we continue to seek innovative solutions to address the challenges of our time, the straw charcoal making machine shines brightly as a beacon of hope and progress.